CNC加工时铝件容易变形怎么办?
- 分享
- 发布时间
- 2022/4/27
概要
铝合金零件变形的原因有很多,所以在加工过程中,减少变形的措施就显得尤为重要。下面这篇文章讲一下在CNC加工过程中防止铝件容易变形的一些措施。

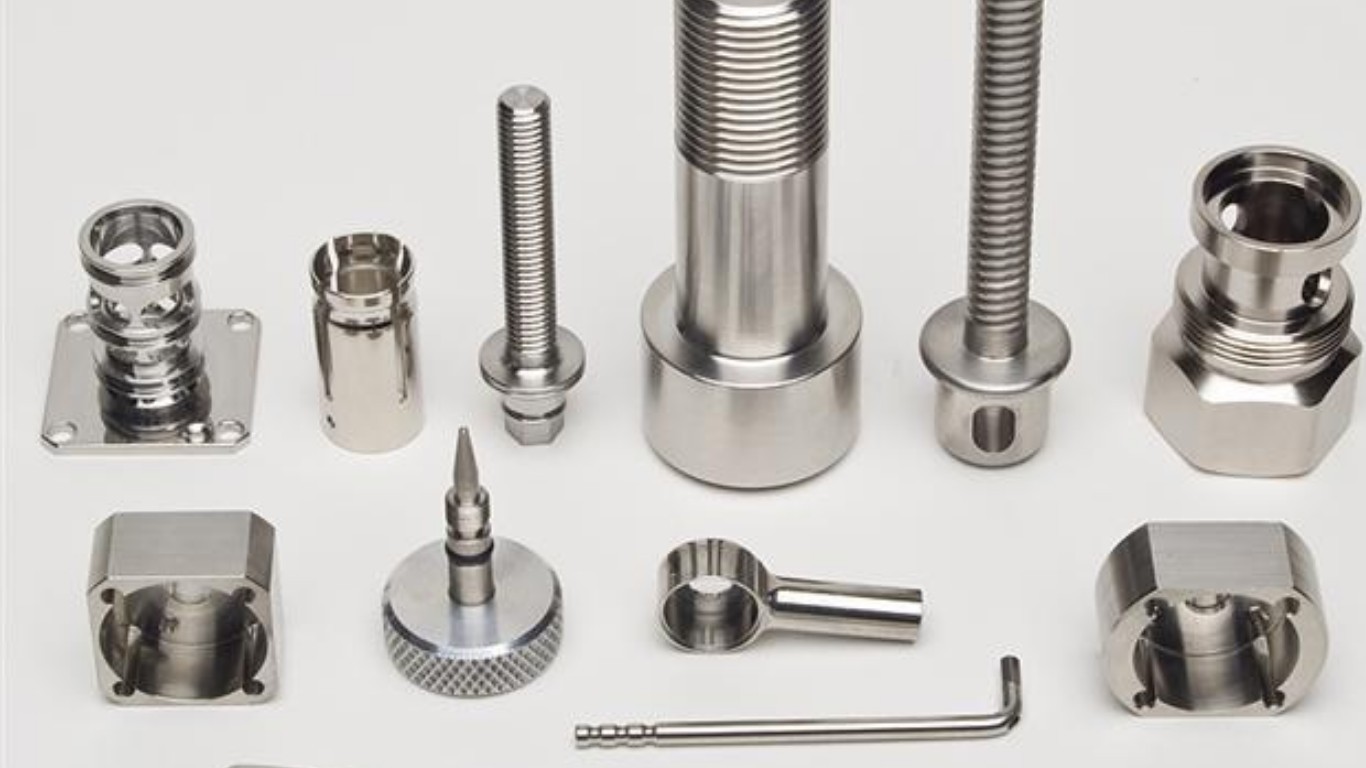
铝是一种活泼的金属,铝是地壳中含量最丰富的金属元素。航空、建筑、汽车三大重要产业的发展要求材料性能具有铝及其合金的独特性能,极大地促进了这种新型金属铝的生产和应用。
由于铝合金零件热膨胀系数大,薄壁加工时容易变形。特别是采用自由锻毛坯时,加工余量较大,变形问题更为突出。
CNC铝合金零件变形的原因有很多,与材料、零件形状、生产条件、切削液性能等有关。
CNC加工时,铝件材质容易变形怎么办?变形的原因主要有以下几个方面:毛坯内应力引起的变形、切削力引起的变形、切削热引起的变形、夹紧力引起的变形。
因此,在加工过程中,减少加工变形的措施就显得尤为重要。主要有以下几个方面:降低毛坯内应力,提高刀具切削能力,合理选择刀具几何参数,改进刀具结构,改进工件装夹方式,合理安排工序
减少加工变形的工艺措施
1、降低毛坯内应力
自然或人工时效和振动处理可部分消除毛坯的内应力。前处理也是一种有效的处理方法。对于毛坯,由于余量较大,加工后的变形也较大。
如果对毛坯多余的部分进行预处理,减少各部分的余量,不仅可以减少后续工序的加工变形,而且经过一段时间的预处理后,可以释放一部分内应力.
2.提高刀具切削能力
刀具的材料和几何参数对切削力和切削热有重要影响。正确选择刀具对于减少零件的加工变形非常重要。
(1)刀具几何参数的合理选择。
耙角:在保持刀片强度的条件下,耙角被适当地选择更大,一方面可以磨碎边缘,另一方面,它可以减少切割变形,使其成为排屑顺畅,进而降低切削力和切削温度。切勿使用负前角的刀具。
后角:后角的大小直接影响后刀面的磨损和加工表面的质量。切削厚度是选择后角的重要条件。
粗铣时,中干进给量大,切削负荷大,发热量大,要求刀具有良好的散热条件。因此,后角应选择较小的。精铣时,要求切削刃锋利,减少后刀面与加工面的摩擦,减少弹性变形。因此,后角应较大。
螺旋角:为使铣削顺畅,减小铣削力,螺旋角应尽量大。
主偏角:适当减小主偏角可以改善散热条件,降低加工区域的平均温度。
(2)改进工具结构。
减少铣刀齿数,增加容屑空间。由于铝材塑性大,加工时切削变形大,需要较大的容屑空间,因此容屑槽底圆弧应大,铣刀齿数宜少。
精细研磨的牙齿。刀齿刃口粗糙度值应小于Ra=0.4um。新刀使用前,应先用细油石在刀齿前后轻磨几下,以消除磨齿时留下的毛刺和细小锯齿。这样,不仅可以降低切削热,而且切削变形也比较小。
严格控制刀具的磨损标准。刀具磨损后,工件表面粗糙度值增大,切削温度升高,工件变形量增大。
因此,除了选用耐磨性好的刀具材料外,刀具磨损标准不应大于0.2mm,否则容易产生积屑瘤。切削时,工件温度一般不应超过100℃,以防变形。
3、改进工件装夹方式
对于干刚性差的薄壁铝制工件,可采用以下装夹方法来减少变形;
(1)对于薄壁衬套零件,如果采用三爪自定心卡盘或弹簧卡盘径向夹紧,加工后一旦松开,工件难免发生变形。这时应采用压入刚性较好的轴向端面的方法。
(2)
(3)定位零件内孔,制作螺纹心轴,插入零件内孔,压上盖板端面,然后用螺母拧紧。加工外圆时,可避免夹紧变形,从而获得满意的加工精度。
(2)加工薄壁、薄板工件时,最好用真空吸盘获得均匀分布的夹持力,然后用少量切削加工,可以很好地防止工件变形。
此外,还可采用现场填充法,为增加工件的工艺刚性,可将材料填充到工件内部,以减少工件在装夹和切削时的变形。
例如,将含有3%~6%硝酸钾的尿素熔体倒入工件中,加工后将工件浸入水中或洒香精,即可将填料溶解倒出。
4、合理安排流程
高速切削时,由于加工余量大,断续切削,铣削过程中常产生振动,影响加工精度和表面粗糙度。因此,CNC高速切削加工过程一般可分为粗加工、半精加工、清角、精加工。
对于精度要求高的零件,有时需要进行二次半精加工,然后进行精加工。零件粗加工后可自然冷却,消除粗加工产生的内应力,减少变形。粗加工后留下的余量应大于变形量,一般为1~2mm。
精加工时,零件的精加工表面应保持均匀的加工余量,一般为0.2~0.5mm,使刀具在加工过程中处于稳定状态,可大大减少切削变形,获得良好的表面加工质量,并确保产品的准确性。
以上介绍了铝件在CNC加工过程中容易变形的解决方法。如果您对以上问题有疑问或需要定制CNC铝件,请联系我们。
ZHONGKEN 是中国专业的定制 CNC 加工零件供应商。我们一直致力于精密机械零件加工、模具零件加工、铸造、钣金零件加工、出口。多年来,我们一直为海外客户提供高精度的机加工零件和优质的服务,深受海外客户的信赖和支持。